
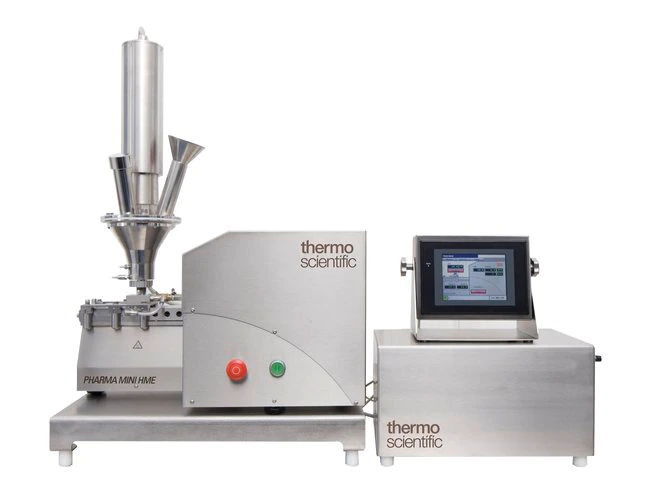
The Thermo Scientific™ Pharma mini HME is a GMP compliant conical micro compounder for Hot Melt Extrusion in research and development in the pharmaceutical industry. When developing new drugs, shortening time-to-market and reducing waste of expensive API's and overall development costs provide a distinct competitive advantage. Hence, quick and early assessment of new API/excipient formulations is critical. Hot melt extrusion and continuous processing can lead to speedier formulation development and cost efficient production. The Thermo Scientific Pharma mini HME allows users to identify the right drug candidates for hot melt extrusion by compounding as little as three grams of material.
With the Pharma mini HME, we offer a micro twin-screw compounder which requires as little as three grams of total material to identify the right drug candidates for hot melt extrusion. The compounder with conical co- or counter-rotating screws is designed to minimize waste and reduce downtime necessary for cleaning.
- Requires only 3g (4mL) of material for compounding
- Small footprint, fanless design with sperate, touch-screen control for operation in fume cabinet or glove box applications
- Removable and exchangeable product contact parts for quick and easy cleaning
- IP 54 for protection against dust and water allows the Pharma mini HME to be spray-washed
- Useable as small-scale production unit for throughputs of 100g/h
- Touch screen control with user levels and password protection
- Data logging software as option to record temperatures, torque, and screw speed
- Optional batch conversion kit to use the Pharma mini HME as small batch mixer
- Complementary workflow solution when coupled with the Thermo Scientific HAAKE™ MiniJet™ injection molder
Materials:
- Pharmaceutical ingredients (API's)
- Excipients
- Medical polymers
- Drug delivery systems
- Soft gels
Applications:
- Hot melt extrusion
- Medical devices
- Implants
- Controlled drug release
- Handling and processing of highly potent API's in a glovebox
A small footprint reduces clean room volumes, and lower ingredient consumption reduces handling and operator exposure.